Copper is a valuable metal used in many residential, commercial, and industrial products. From wiring and consumer electronics to HVAC systems and electric vehicles, copper is an essential element necessary to produce such products. Copper mining is a complex process and water is its lifeblood. It allows for the separation and recovery of salable copper. Throughout the milling and flotation cell processes, water consumption is particularly high. In fact, for every one ton of copper sulfide ore being processed, over double the amount of water is required throughout the crush-grind-flotation-concentrate circuit. Poor control of the mine’s water supply can negatively impact process run-time, leading to constrained production levels and hurting the bottom line. Additionally, as a mine ages, copper ore grades generally decline. To maintain target recovery rates, mines must process more material, called ore tons. As time passes, this adds to the mine’s overall water consumption.
Around the world, mining companies are working to develop a more sustainable production method to address environmental concerns and maintain stable operations. Chile is home to the world’s largest copper mine and it is the country’s largest water consumer. In 2018, the mine underwent an expansion project to implement a desalination plant and added a necessary pipeline to feed the operation. The goal was to operate entirely on desalinated water by the year 2030. In 2020, 10 years ahead of the planned schedule, that goal was achieved. The mine’s new water source is pumped over 3,100 meters above sea level to a reservoir near the mine. From there, the water is then delivered to a pond next to one of the mills. Water flow from the reservoir is then delivered through a 36-inch discharge line and is controlled with an 18-inch globe valve. The pond is the sole water supply to the mill and concentrator.
Greater process control is a hallmark of REXA’s Electraulic™ actuators. Our actuators provide a more precise and accurate performance than pneumatics and are more reliable than traditional hydraulic technologies. This mine’s location is remote, arid, and the ambient temperature can drop below 0°C in the winter. For this project, the mine had considered pneumatic actuators. The decision was made to not use the pneumatics because of their marginal positioning accuracy and reliability. To keep the concentrator process running, it is crucial that there is water present. Mine operators chose to rely on REXA Electraulic™ Actuation as the final control element to control water flow rate and emergency shutoff. Upon an unexpected loss of power, the linear actuators, equipped with accumulator bottles, produce up to 20,000 lbf (89,000 N) of thrust that can safely close the valves using pressurized nitrogen.
In 2021, desalinated water is now used to supply all the copper mine’s water requirements. REXA actuators played a vital role in this successful four-year transition. Our self-contained Electraulic™ system locks the cylinder in place, when no movement is required, minimizing wear and tear on moving components and eliminating unnecessary power consumptions. REXA Electraulic™ actuators have been engineered for use for constant modulating duty cycle and precise positioning independent of load variation. REXA’s actuation package supports various control system protocols including HART (Highway Addressable Remote Transducer) and Ethernet IP. Pipeline flow control is an excellent example where reliable positioning performance is necessary to prevent and minimize unscheduled downtime.
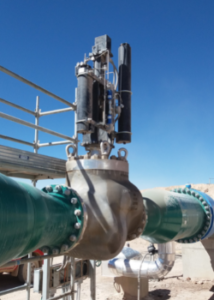
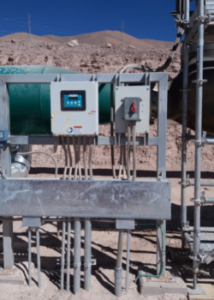
Download the full success story & learn more
Click the button below to download the full success story! Interested in learning more about our solution for other applications? Click here to further explore REXA in other applications.