Success Story: Steam Turbine Actuator Retrofit
Hydroprocessing in the O&G refining industry refers to two separate, yet similar, processes: hydrocracking and hydrotreating. The hydrocracking process converts a variety of petroleum fractions, including oil recovered from solvent extraction of petroleum residues, into more valuable, lower-boiling fuel products. Hydrotreating refers to the process of upgrading the quality of petroleum distillate fractions, such as catalytic and thermally cracked distillates, by decomposing the contaminants with a negligible effect on the boiling range of the feed.
Hydroprocessing units include applications such as charge pumps and recycle compressors, driven by steam turbines. Steam turbines convert thermal energy to rotational energy-ultimately controlling the input speed or power of the driven device. Maintaining reliable and repeatable control of the turbine is essential for refineries to achieve efficiency goals and eliminate costly downtime for maintenance. This is possible by identifying and implementing the right actuation technology.
REXA recently conducted a steam turbine actuator retrofit on a Nuovo Pignone steam turbine driving a hydrogen recycle compressor at a refinery in Mexico. The OEM actuator was the original Nuovo Pignone system, which consisted of a pilot valve and power piston. This actuator required an external oil supply from the turbine oil skid
(pump). One of the main issues with this actuator type is its susceptibility to oil contamination and varnishing, which causes internal stiction. The actuator exhibited poor control and “hunted” for position, ultimately leading to large and unwanted RPM swings, as well as costly nuisance trips.
Refinery personnel met with REXA to develop the right solution. Following review of all the issues, REXA proposed the “Rotating Equipment Total Integrated Solution” package. This all-inclusive upgrade solution includes onsite evaluation, engineered actuator mounting hardware, and installation drawings, TAR supervision and support, both mechanical and electrical integration/calibration, as well as on-site REXA product training. By utilizing the self-contained design of Electraulic™ Actuation, the need for the external oil supply to the OEM actuator was eliminated. All segments of the REXA hydraulic circuit are positive pressure. The oil inside the actuator is never exposed to atmospheric conditions and excessive heat, ensuring no contamination or varnishing. Replacing the old flyball governor and installing our Electraulic actuators allowed tighter speed (RPM) control. This also enabled fully automatic startup of the machine from the control room, meaning they were able to start the unit and put it online
consistently without variants in operator methods. With the implementation of the digital speed controller and our actuator to control the process loop, our customer now has the capability to fully modify the setpoint from the control room from 0-100% speed, a much-needed upgrade from the analog control loops of the older OEM equipment.

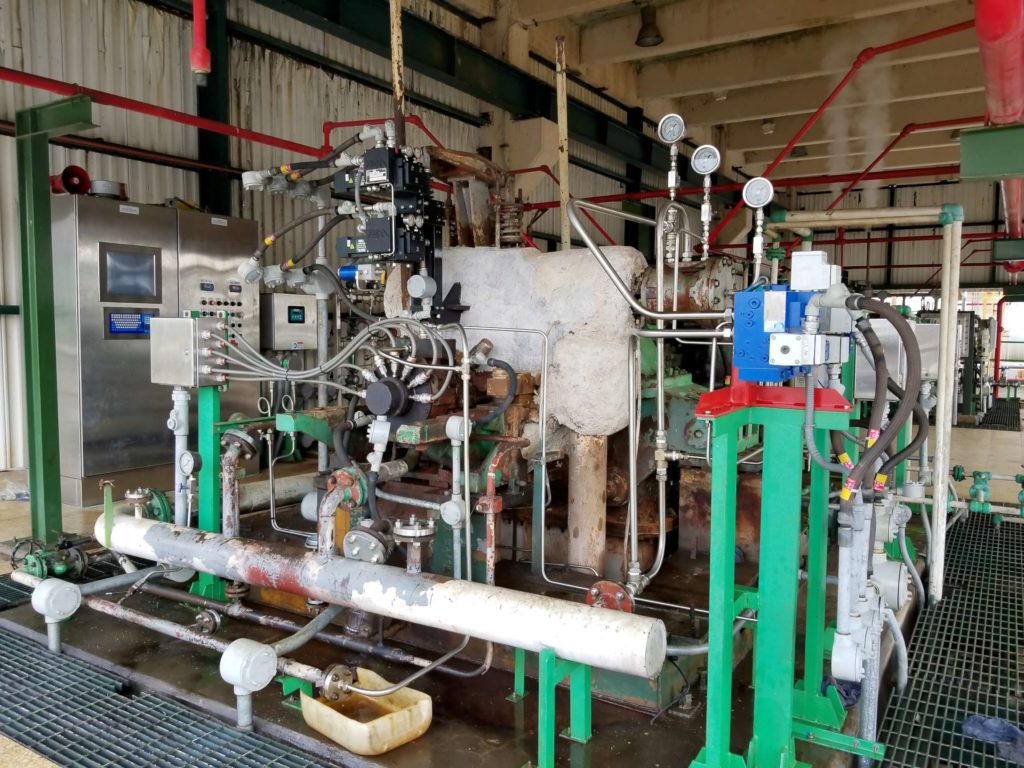
Literature
Click here to download the full Success Story!